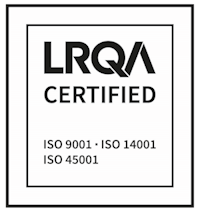
Quality Management
Quality, as we use it every day...
Dickow QM
QUALITY POLICY
All processes at our company that have a direct or indirect influence on the development of the products are precisely defined. The fulfilment of receivables from customers are ensured. External and internal influencing factors as well as the interests of other parties are taken into account.
Dickow QM
Certifications
At our company, we place a high value on quality and safety. This is reflected in our commitment to maintaining the highest standards in these areas. To this end, we regularly have our products and processes certified by independent testing bodies. These certifications confirm that we adhere to the highest standards in terms of safety, environmental compatibility, and efficiency.
Our certificates span a comprehensive range of areas, including quality management, environmental protection, and product safety. Each certificate is granted in accordance with rigorous criteria and is subject to periodic review to ensure continuous compliance with the highest standards.
Our overview includes all current certificates that demonstrate our commitment to excellence and transparency.
Dickow QM
MEASURE AND CHECK
Product characteristics are tested at appropriate stages of the development process, to verify their conformity with the relevant requirement.
For this purpose, product tests including the definition of acceptance criteria are planned and carried out. The test results are recorded, in order to make the proof of conformity of the products with the acceptance criteria comprehensible and to document them.
Dickow QM
HE MATERIAL CONFUSION TEST
The quantitative and non-destructive determination of the alloying elements of metallic materials is carried out in a time-saving manner and without time-consuming sample preparation, using X-ray fluorescence spectrometry XRF.
With a handheld analyzer, fast results are available for both incoming goods inspection and documented PMI tests.
Dickow QM
THE PENETRATION TEST
The effectiveness of the process is based on the minimal surface tension of the red dye and excellent creep ability. Due to these properties and the capillary effect, the agent penetrates even the smallest imperfections.
The developer, applied after intermediate cleaning, draws the dye liquid to the surface and visualizes the defects.
Dickow QM
THE HARDNESS TEST
Hardness testing is by far the most widely used material testing method for testing metallic materials and compounds.
The purpose of hardness testing is, to determine comparable performance indicators of the deformation resistance of the surface of a material.
Whether standardised test methods according to Brinell, Vickers or Rockwell, but also non-standardised methods such as the VCI method, result in a comparable figure that does not contain any clear material property, but can be applied in various ways.
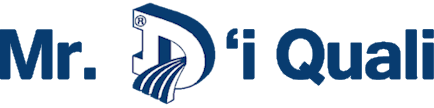
➢ is the quality conscience of DICKOW PUMPEN
➢ pays particular attention to the satisfaction of our customers
➢ is based on the highly qualified services of all DICKOW employees
The 10 Commandments of our Quality Management:
1
You should know the needs and expectations of our customers.
6
You should always guarantee the high quality of our products.
2
You should ensure the customer requirements of our products.
7
You should point out quality problems and develop reliable solutions.
3
You should seek and maintain dialogue with our customers.
8
You should check your quality awareness regularly.
4
You should consider qualified suppliers as our partners.
9
You should constantly rethink the quality processes and constantly improve them.
5
You should consider the interests of other parties as well as external and internal influencing factors.
10
You should ensure the functionality of the QM system.